I find medieval textile production fascinating, with its unique blend of skill and tradition. The process began with raw materials like wool, carefully sorted and washed to achieve the perfect quality. Spinning, using tools like spindle whorls or later spinning wheels, transformed these fibers into fine yarn. Weaving was a true art form, with horizontal looms and foot pedals working together to create fabric. The dyeing process was equally intricate, relying on natural mordants and vibrant colors sourced from plants like woad. Textiles played a significant role in medieval society, not only clothing people but also showcasing social status and devotion, adorning everything from homes to churches. Each step in the process reveals more about this rich and intricate craft.
Raw Materials
In medieval textile production, wool was the primary raw material, carefully sorted by its coarseness to determine its specific use. I've often been impressed by the precision required at each stage of wool production. The process began with washing the wool – using soap, hot alkaline water, and lye – to remove grease, oils, and dirt. This thorough cleansing was vital for achieving high-quality textiles.
The next step involved manually beating the wool with sticks, typically willow branches, to remove any remaining foreign matter. This labor-intensive process prepared the fibers for dyeing and ensured a uniform texture. Dyeing was an intricate process; preliminary dyeing used natural mordants to lock in vibrant colors, with processes like woad dyeing taking up to three days to guarantee color fastness.
Greasing wool before further processing was another critical practice. Substances like butter or olive oil were applied, providing a protective layer that safeguarded the fibers during the harsher stages. Sometimes, lanolin, the natural grease found in wool, was left intact to act as a lubricant. This meticulous preparation of raw materials laid the foundation for the textile industry's success, even influencing the quality of foreign cloth imported into medieval markets.
Spinning Techniques
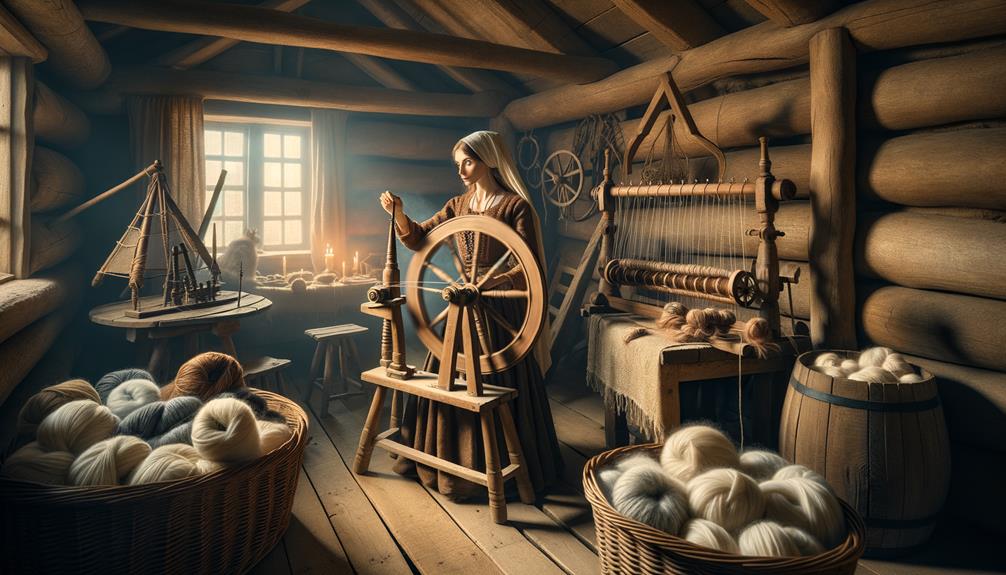
Medieval spinning techniques, which involved the meticulous use of spindle whorls crafted from bone, wood, or clay, demonstrate the ingenuity and dexterity of medieval artisans. Watching a skilled spinner hand-twist wool fibers into yarn is mesmerizing. They had a way of rhythmically adding fibers, creating a continuous thread with remarkable precision. The variations in spindle whorls allowed for different yarn thicknesses, catering to a wide array of textile needs.
The introduction of spinning wheels in the late Middle Ages revolutionized yarn production. These wheels dramatically increased the speed and efficiency of spinning, transforming the textile industry. Among the fibers spun, wool was predominant, but flax and silk also played significant roles. Each fiber required a unique approach; for instance, flax needed to be wetted to ease the spinning process, while silk demanded a delicate touch due to its fine nature.
Reflecting on these medieval spinning techniques, I marvel at how these artisans balanced tradition and innovation. They not only met the demands of their time but laid the groundwork for future textile advancements.
Weaving Processes
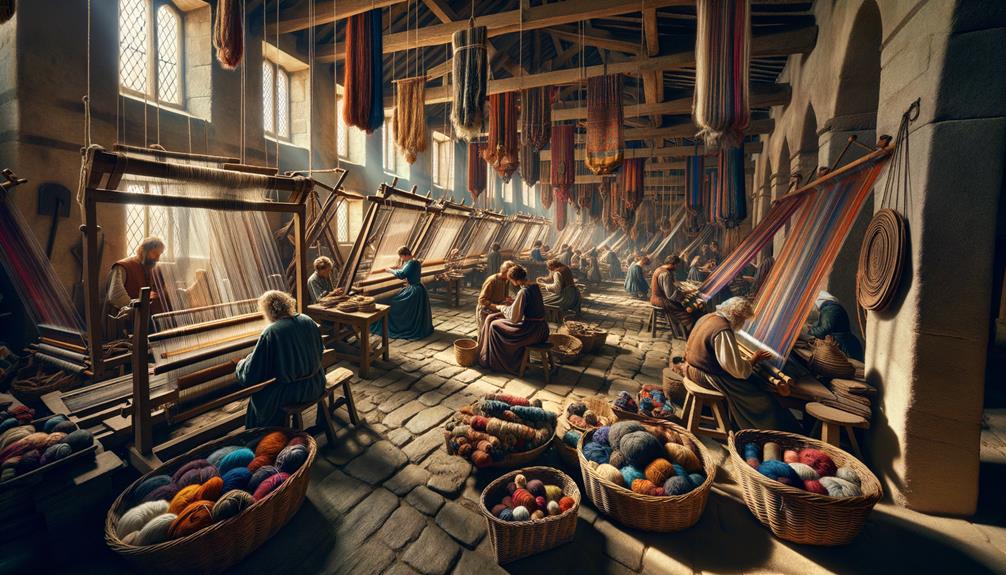
Weaving, a delicate interplay of threads, transformed simple fibers into vibrant textiles through the skilled hands of medieval artisans. The weaving processes of this era were truly groundbreaking. By drawing weft threads through the perpendicular warp threads, artisans could create a diverse array of fabrics. The shift from vertical to horizontal looms marked a significant milestone in cloth production, enhancing efficiency and precision. These horizontal looms, often mechanized with foot pedals and shuttles, allowed weavers to produce a piece of fabric more swiftly and with greater consistency.
Observing these weavers at work, one can't help but be impressed by their dexterity and attention to detail. By varying the weights of the warp and weft threads, they achieved different textures and strengths in the finished cloth, catering to the needs of their time. Each loom was a testament to innovation, embodying the ingenuity of medieval history. The finished products, whether simple or elaborate, showcased the weavers' expertise and the sophisticated technology they employed. Reflecting on these processes, it's clear that the evolution of weaving was not just about making cloth but about pushing the boundaries of what was possible in textile production.
Dyeing Methods
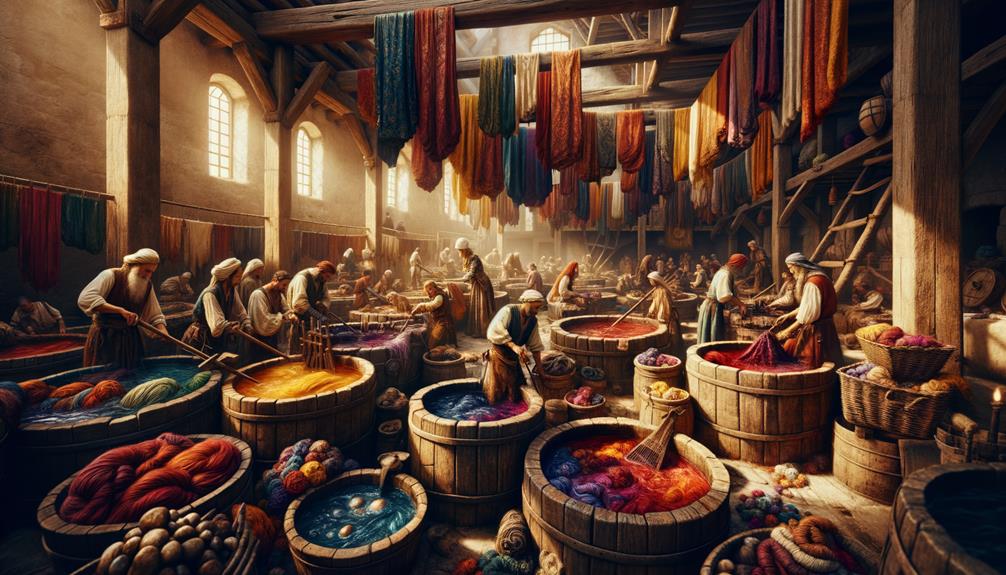
As I admired the intricate weaving processes, I couldn't help but notice how the vibrant hues of the textiles owed much to the meticulous dyeing methods employed by medieval artisans. These methods, rich with tradition, utilized imported dyestuffs like woad, madder, and weld, each contributing to the vibrant colors that defined medieval Europe.
The process of textile dyeing was a complex, multi-step affair. Cloth dyers often relied on mordants to secure colors and enhance color fastness, guaranteeing the hues remained vivid through wear and wash. Each region had its own dyeing traditions, often preferring certain colors that became synonymous with local identity.
Dyestuff | Color Produced | Region of Popularity |
---|---|---|
Woad | Blue | Northern Europe |
Madder | Red | Southern Europe |
Weld | Yellow | Western Europe |
Indigo | Deep Blue | Imported widely |
Cochineal | Crimson | Later periods |
Reflecting on these dyeing methods, it's clear that the final appearance and market value of textiles were heavily influenced by these vibrant hues. The artisans' dedication to their craft not only created beautiful fabrics but also ensured that their work stood the test of time, both in durability and historical significance.
Textile Uses
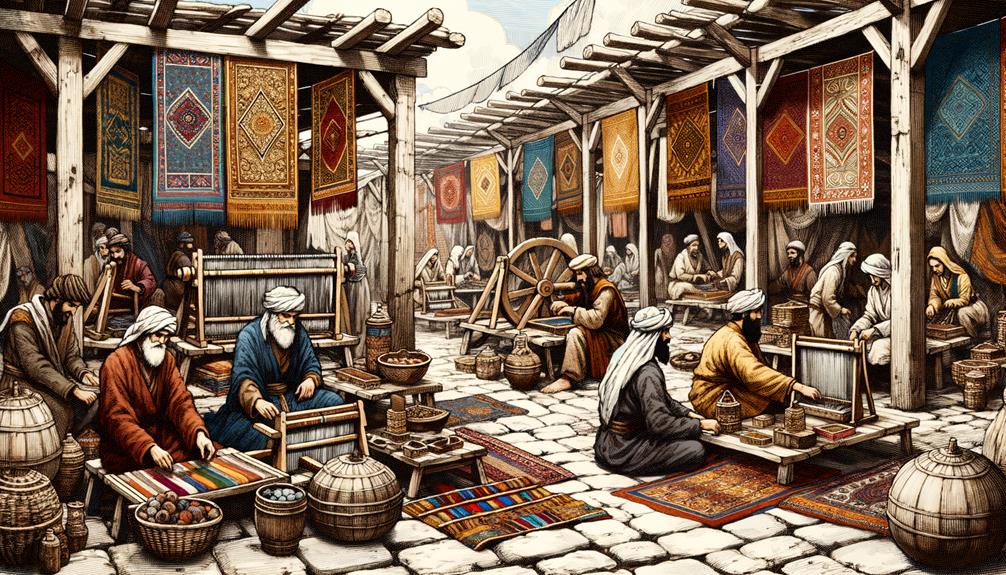
Textiles in the Middle Ages played a multifaceted role, serving not only as essential household items and clothing but also as significant symbols of social status and religious devotion. In daily life, medieval cloth was omnipresent, from the bedding that provided warmth on cold nights to the curtains that offered privacy.
In urban centers, cloth production flourished, particularly in the late Middle Ages. The introduction of the spinning wheel and the fulling process, which cleaned and thickened fabric, revolutionized textile production. The quality of fabric often indicated social standing, with nobles adorning themselves in luxurious textiles and common folk wearing simpler, coarser cloth.
Religious institutions adorned altars with richly embroidered cloths, and priests wore vestments crafted with elaborate designs. These textiles, imbued with spiritual significance, found their way into ceremonial banners and tapestries, reflecting religious devotion.
The versatility and durability of medieval textiles made them a staple in trade, with textiles being exported far and wide, cementing their role in the economy. As a result, the full spectrum of medieval life was intertwined with fabric, each thread telling a story of its time.
Frequently Asked Questions
How Were Textiles Made in Medieval Times?
I've always been fascinated by the art of textile production in medieval times. The process was meticulous, with wool being sorted, cleaned, and dyed before being woven and finished through various techniques like fulling, shearing, and napping. The craftsmanship of medieval textile makers laid the groundwork for later innovations in the field.
What Materials Were Medieval Clothes Made Of?
Diving into the world of medieval fashion, I uncover three primary materials used to craft clothes: wool, linen, and silk. Wool's versatility made it a staple, while linen provided a breathable fabric, and luxurious silk adorned the wealthy, often dyed in vibrant hues.
Who Made the Clothes in Medieval Times?
In medieval times, skilled artisans, clothiers, and textile workers crafted clothes. These skilled professionals, like those in Colchester and Norwich, oversaw the entire process, leaving a lasting impact on society and the landscape.
What Was Produced in Medieval Times?
Reflecting on the past, it's intriguing to see what medieval times produced – from everyday clothing to intricate tapestries. The use of wool, linen, and silk showcased remarkable craftsmanship, reminiscent of the precision we see in modern technology.